Большой проект. Подводная лодка. Продолжение. ч.9.
Наконец-то закончились морозы и проблемы с машиной. И после месячного перерыва я дорываюсь до загородной мастерской со сваркой и большими станками. Выкатывание верхнего абажура.
Склеиваю заготовку для болвана. 2 куска фанеры и 2 куска ДСП:
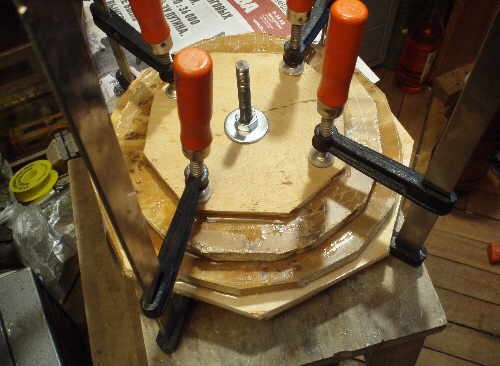
Обтачиваю:
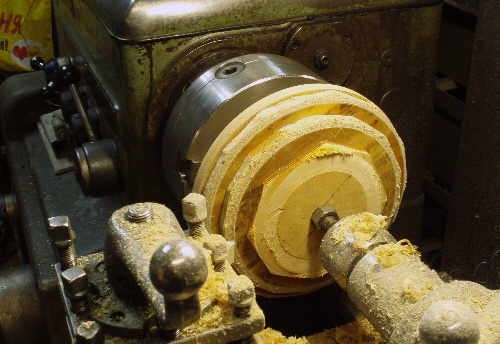
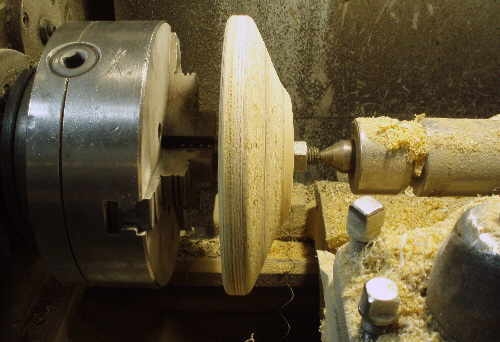
Изготовление давочного ролика:
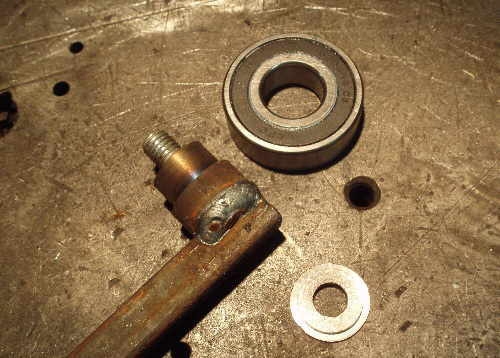
Подшипник (от подохшей перед НГ стиральной машины) попался с довольно толстенькой внешней обоймой, поэтому я не стал напрессовывать наружную радиусную насадку, а непосредственно саму обойму скруглил на большом наждаке и прощлифовал:
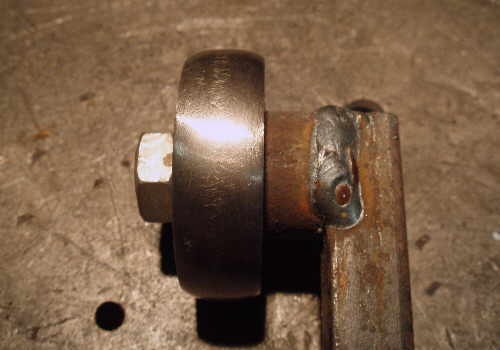
Выкатывание. Мягкое неоцинкованное железо 0,5 мм, несколько промежуточных отжигов горелкой. Все-таки я не настоящий профи по ротационке, и такую большую вещь катаю первый раз. Поэтому избежать складок по краю диска конечно не удалось, но они были успешно побеждены на финишном этапе раскатки, когда ролик уже плотно прижимает металл к болвану:
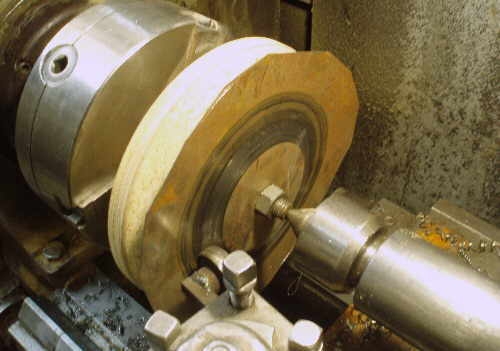
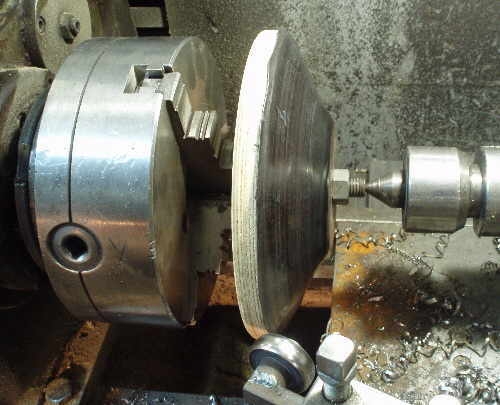
Завальцовка края:
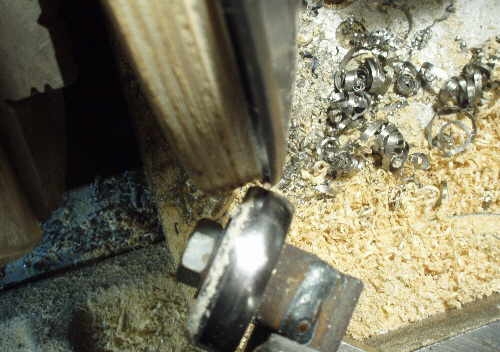
После этого заготовка уже не снимается с болвана, но выход есть. Болван-то деревянный :-) Снова грею край горелкой, чтобы удерживающий буртик на деревяхе частично сгорел. Снимаю готовый абажур. Вкладываю под отвальцованный край кольцо из 1,5 мм стальной проволоки, и аккуратно молоточком загибаю вальцовку. Получается очень жесткий, нетравматичный, и приятно закругленный край, увеличенной толщины по-сравнению с основным металлом изделия (Не знаю как он называется по правильному, но проф. жестянщики так делают на ведрах и пр. посуде ручного изготовления).
Удаление центральной части:
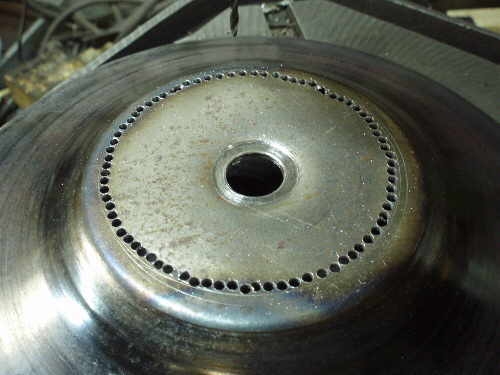
Корпус от автомобильного фильтра для масла:
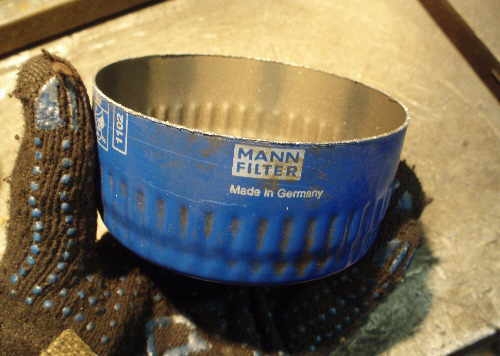
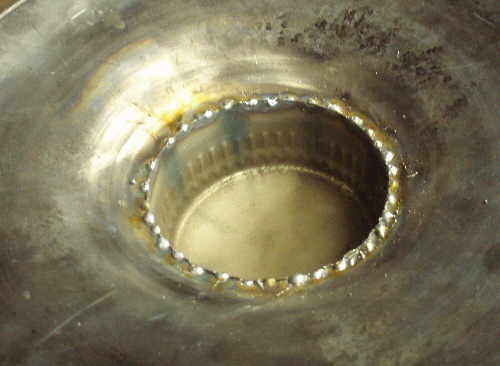
Непросто варить такой тонкий металл даже хорошим полуавтоматом. Главное чтобы сквозных прожогов не было.
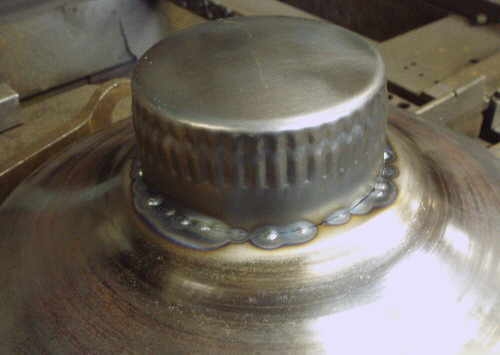
Вертикальная колонна и абажур будут соединяться ажурной грузовой стрелой, как у подъемного крана:
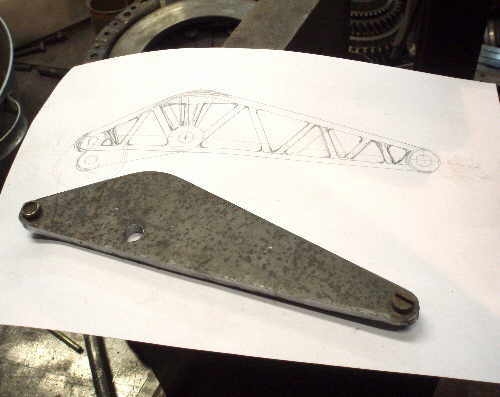
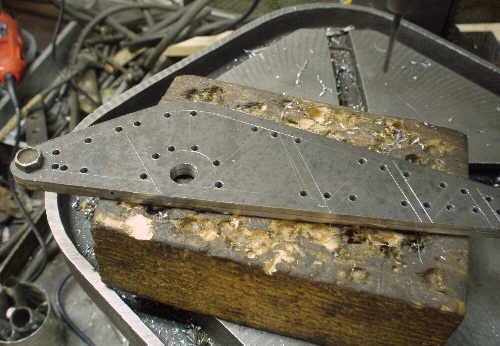
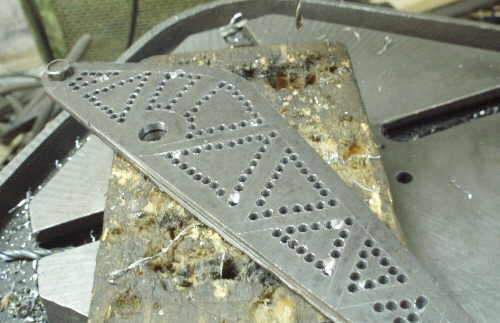
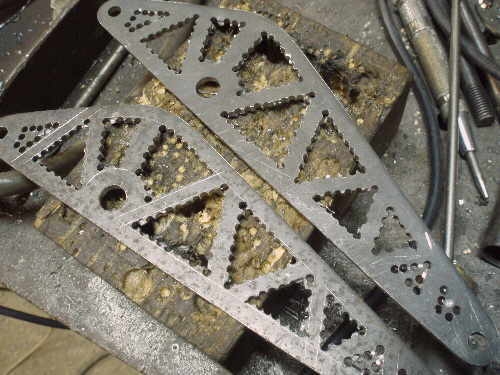
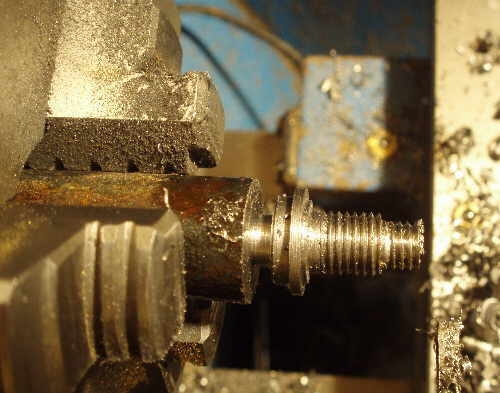
Дальше опять нужна сварка, поэтому откладываю эти заготовочки, и опускаюсьв Нижний Мир
… в общем, к чугунному диску — основанию моей композиции. На нем вдоль края по кругу есть 10 отверстий с расточенным площадками. И у меня есть план ни одно из них не оставить пустым. В каждой площадке будет стоять какая-нибудь интересная и красивая стимпанк-фигня:-)
Ведь для обслуживания и заправки подводной лодки между плаваниями, требуется много всяких сложных механизмов — компрессоры, генераторы и т.п.
Например, что-то типа парового котла, и по сторонам от него два баллона высокого давления.
Крупненькие вентили на баллонах, в отличие от мелких цельно-паяных, можно будет покрутить:

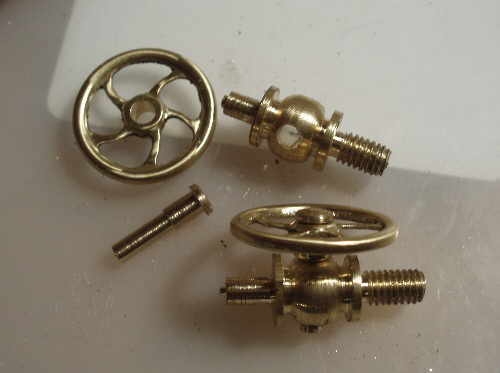
Корпус котла:
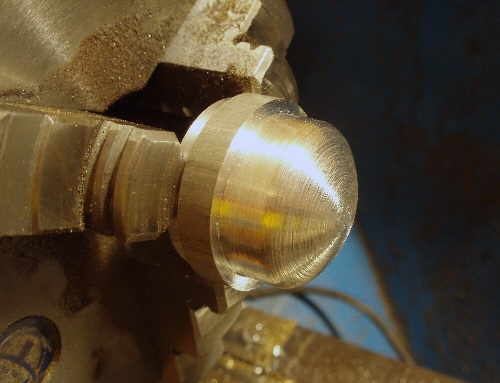
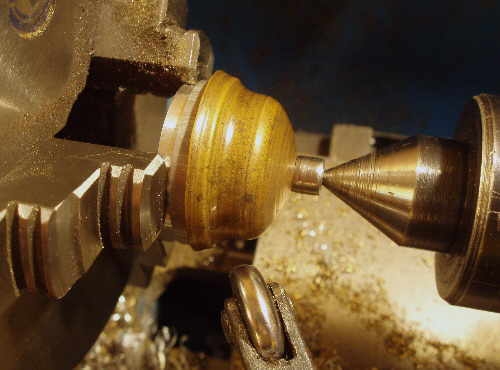
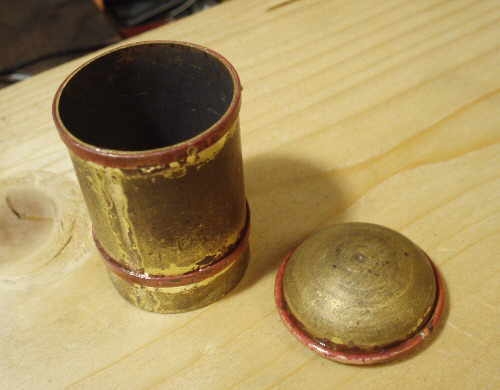
На котле будет настоящее водомерное стекло. Стеклянную трубочку беру от плавкого предохранителя:
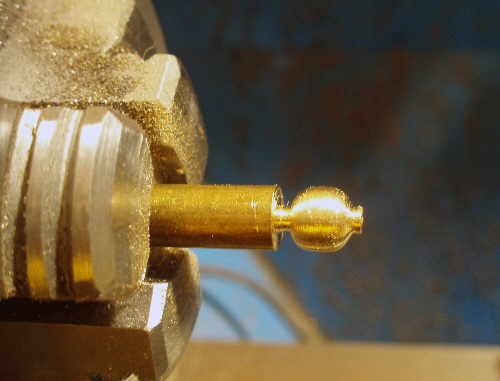
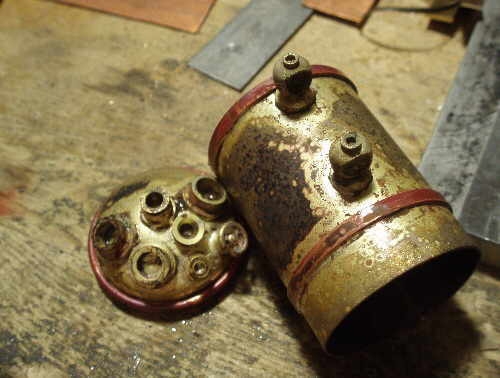
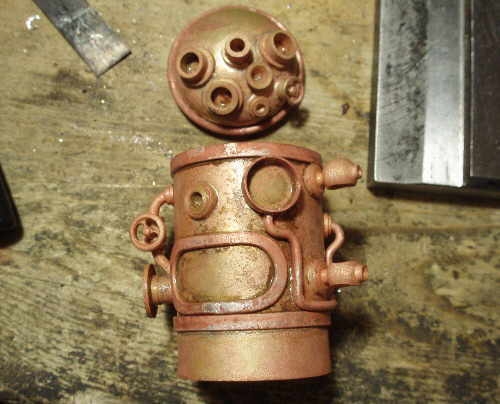
Котел в сборе. Рука набита на флешках, только тут места побольше, есть где разгуляться :-)
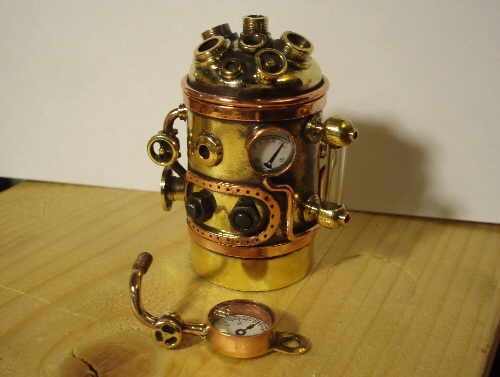
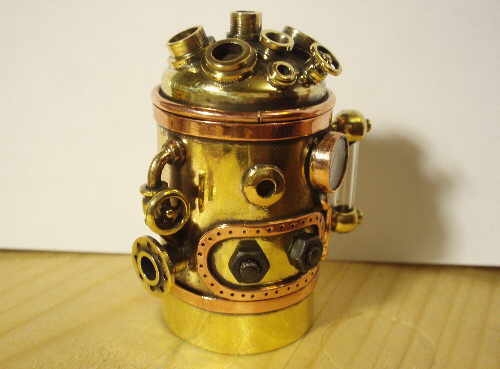
Дополнительный манометр на основном корпусе стапеля:
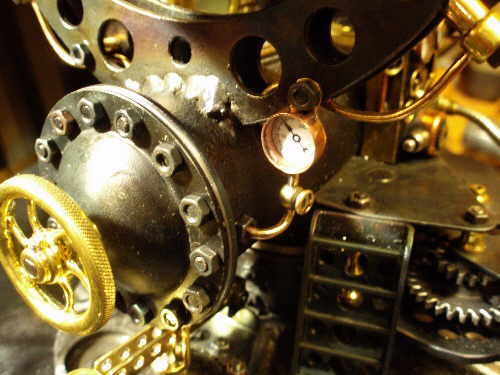
Котел и баллоны соединяются прихотливо изогнутыми трубками. Чтобы медная трубка не сминалась на малом радиусе, гну вокруг специально выточенной роликовой оправки, через несколько промежуточных отжигов. Оправка не дает трубке сплющиваться, расползаться в ширину при сгибании. Таким образом можно обойтись без внутренней забивки песком, канифолью и т.п. веществами, и сохранить правильный профиль трубки на повороте:
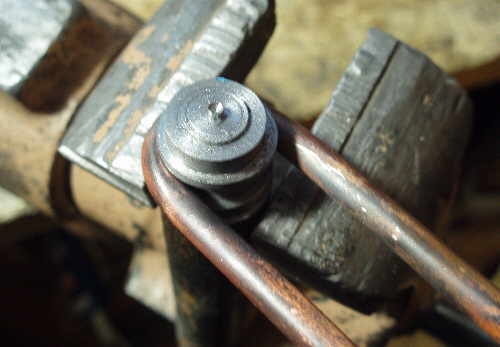
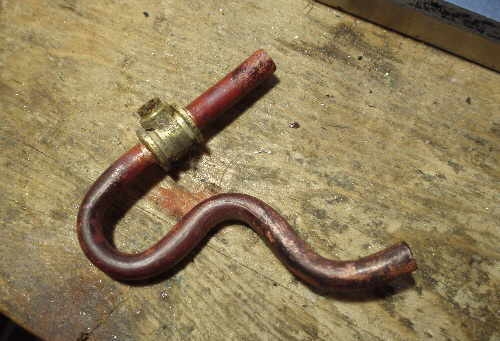
Для разнообразия, эти трубы будут не гладкими, а как бы составлены из отдельных колен. Для имитации стыков напаиваются колечки из мельх. проволоки:
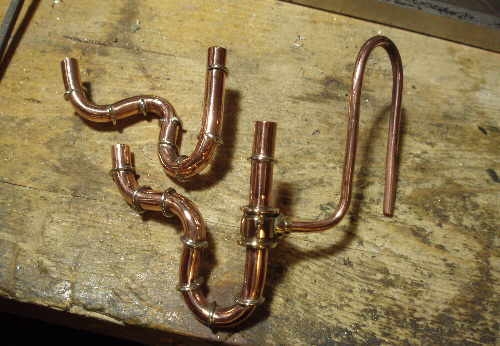
Корпуса «баллонов»:
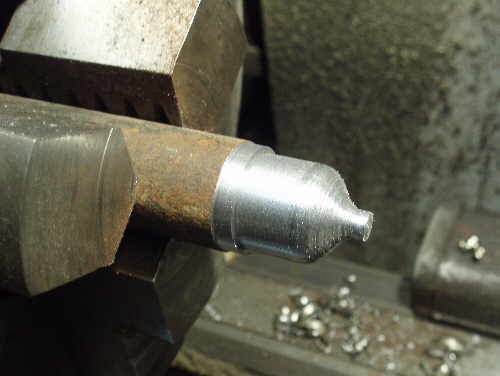
Узел в сборе:
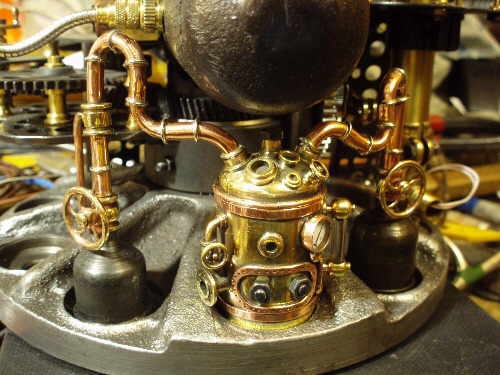
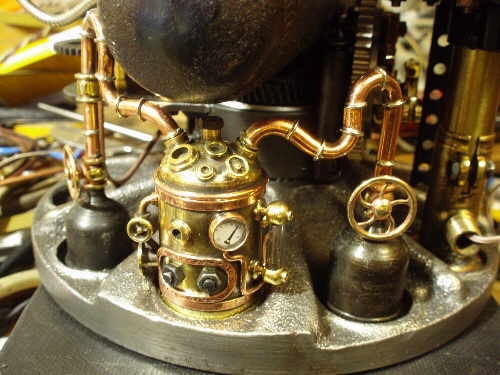
Окончательное соединние трубок с вентилями и крышкой котла произведена на олово, электрическим паяльником.
Теперь незанятыми осталось всего два слота на чугунном диске :-)
Продолжение следует :-)
Предыдущие части ворклога:
steampunker.ru/blog/forsteammaker/5997.html
steampunker.ru/blog/forsteammaker/5998.html
steampunker.ru/blog/forsteammaker/5999.html
steampunker.ru/blog/forsteammaker/6002.html
steampunker.ru/blog/forsteammaker/6006.html
steampunker.ru/blog/forsteammaker/6009.html
steampunker.ru/blog/forsteammaker/6023.html
steampunker.ru/blog/forsteammaker/6095.html
Склеиваю заготовку для болвана. 2 куска фанеры и 2 куска ДСП:
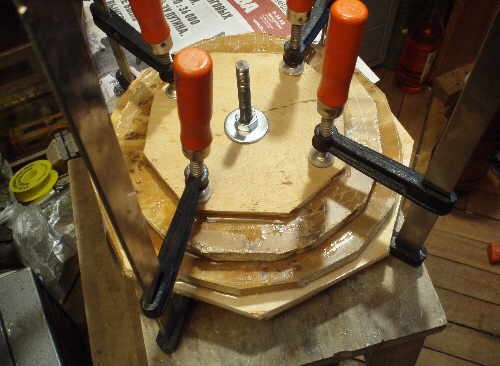
Обтачиваю:
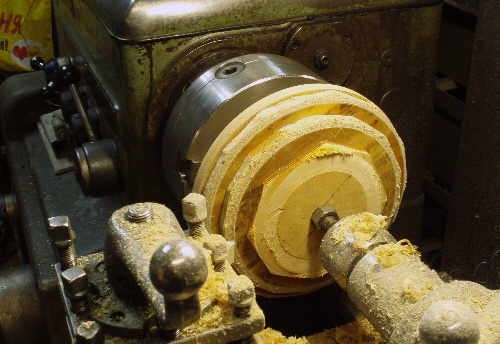
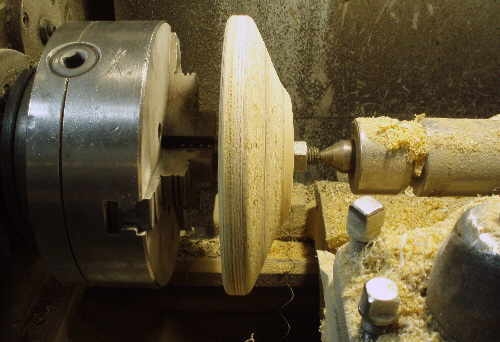
Изготовление давочного ролика:
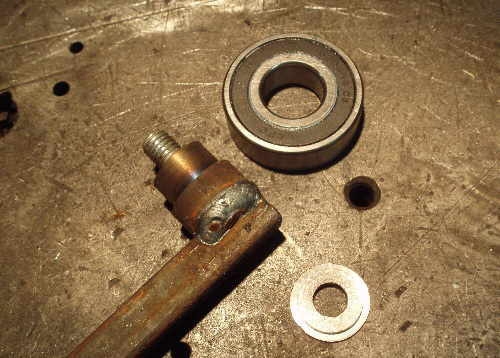
Подшипник (от подохшей перед НГ стиральной машины) попался с довольно толстенькой внешней обоймой, поэтому я не стал напрессовывать наружную радиусную насадку, а непосредственно саму обойму скруглил на большом наждаке и прощлифовал:
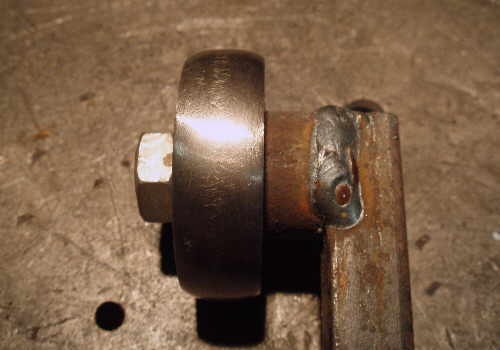
Выкатывание. Мягкое неоцинкованное железо 0,5 мм, несколько промежуточных отжигов горелкой. Все-таки я не настоящий профи по ротационке, и такую большую вещь катаю первый раз. Поэтому избежать складок по краю диска конечно не удалось, но они были успешно побеждены на финишном этапе раскатки, когда ролик уже плотно прижимает металл к болвану:
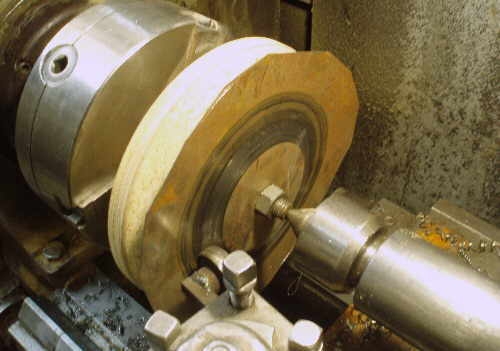
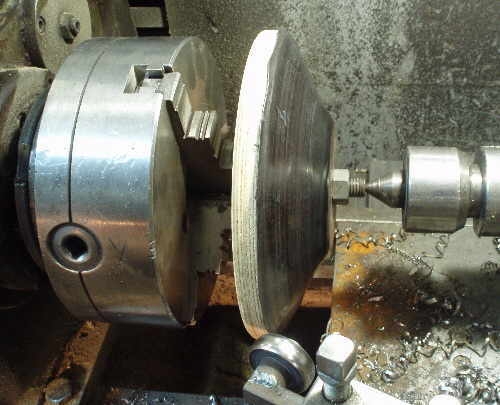
Завальцовка края:
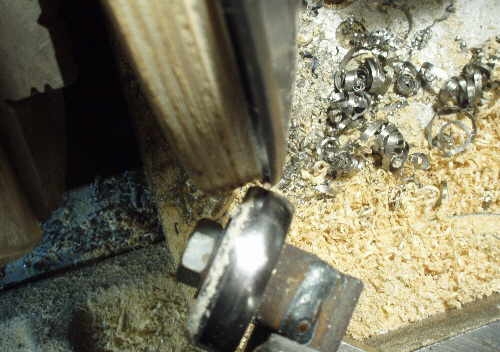
После этого заготовка уже не снимается с болвана, но выход есть. Болван-то деревянный :-) Снова грею край горелкой, чтобы удерживающий буртик на деревяхе частично сгорел. Снимаю готовый абажур. Вкладываю под отвальцованный край кольцо из 1,5 мм стальной проволоки, и аккуратно молоточком загибаю вальцовку. Получается очень жесткий, нетравматичный, и приятно закругленный край, увеличенной толщины по-сравнению с основным металлом изделия (Не знаю как он называется по правильному, но проф. жестянщики так делают на ведрах и пр. посуде ручного изготовления).
Удаление центральной части:
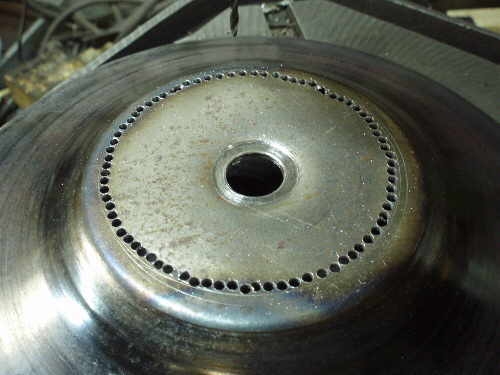
Корпус от автомобильного фильтра для масла:
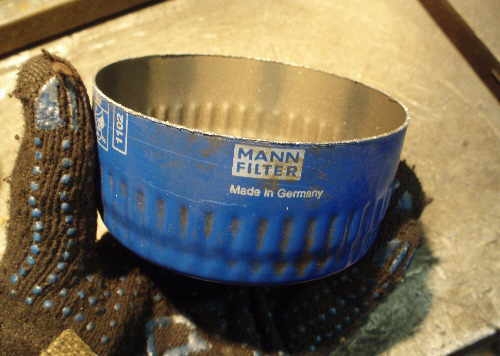
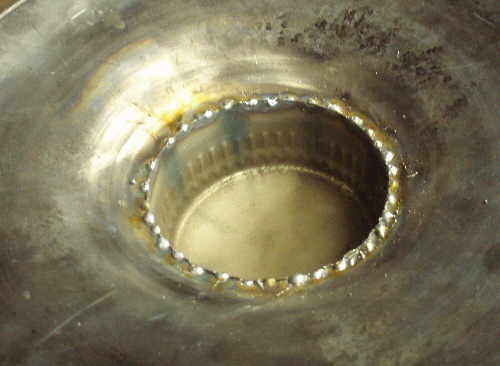
Непросто варить такой тонкий металл даже хорошим полуавтоматом. Главное чтобы сквозных прожогов не было.
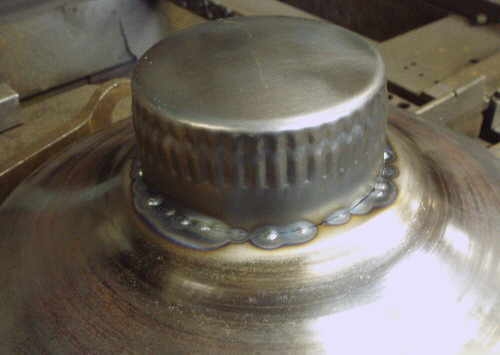
Вертикальная колонна и абажур будут соединяться ажурной грузовой стрелой, как у подъемного крана:
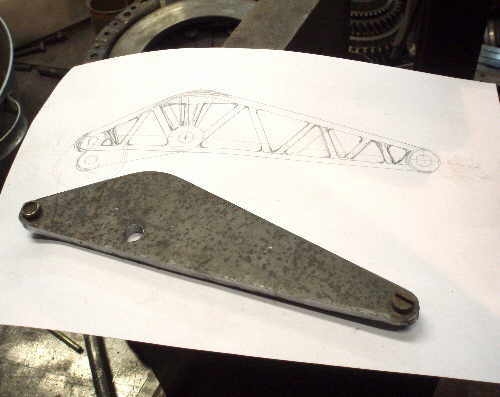
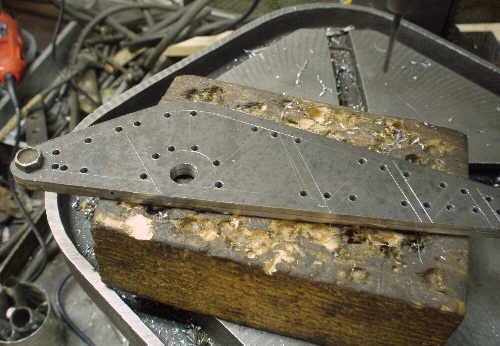
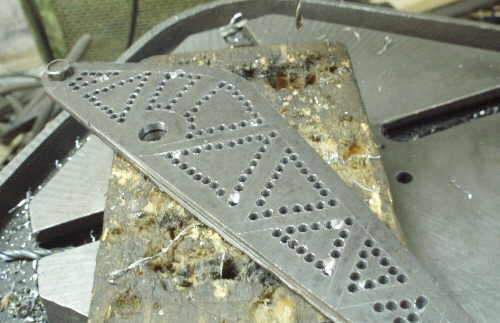
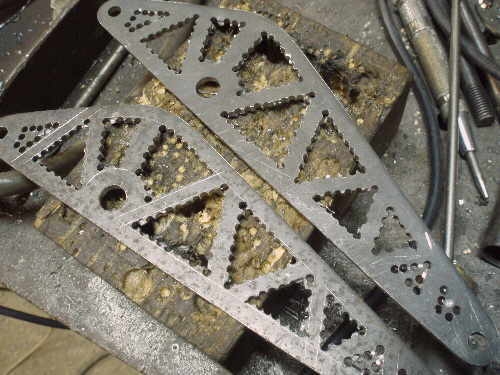
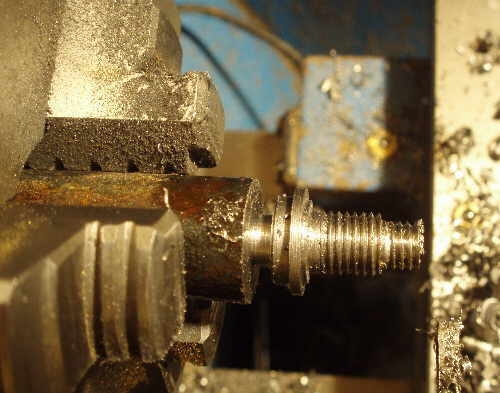
Дальше опять нужна сварка, поэтому откладываю эти заготовочки, и опускаюсь
… в общем, к чугунному диску — основанию моей композиции. На нем вдоль края по кругу есть 10 отверстий с расточенным площадками. И у меня есть план ни одно из них не оставить пустым. В каждой площадке будет стоять какая-нибудь интересная и красивая стимпанк-фигня:-)
Ведь для обслуживания и заправки подводной лодки между плаваниями, требуется много всяких сложных механизмов — компрессоры, генераторы и т.п.
Например, что-то типа парового котла, и по сторонам от него два баллона высокого давления.
Крупненькие вентили на баллонах, в отличие от мелких цельно-паяных, можно будет покрутить:

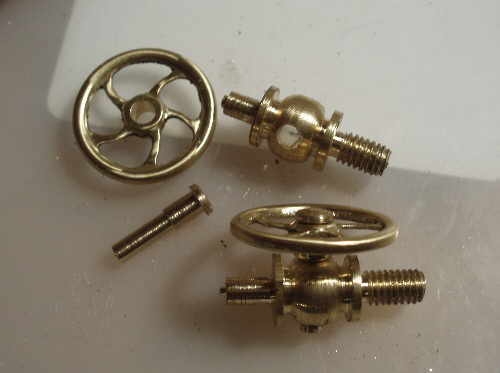
Корпус котла:
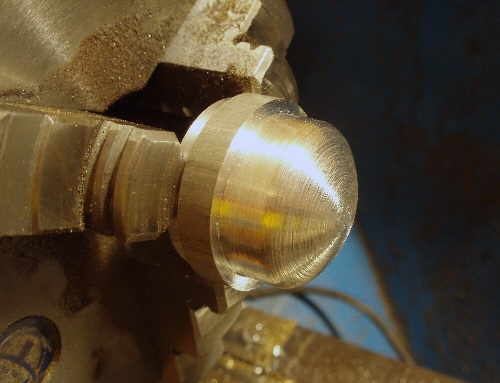
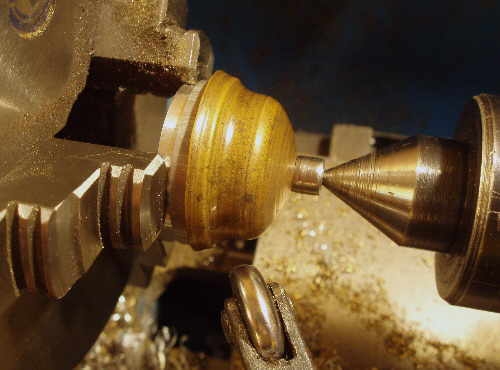
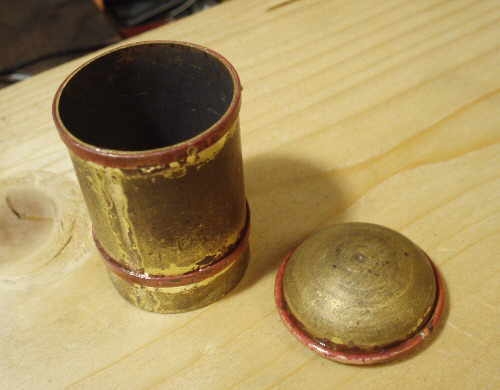
На котле будет настоящее водомерное стекло. Стеклянную трубочку беру от плавкого предохранителя:
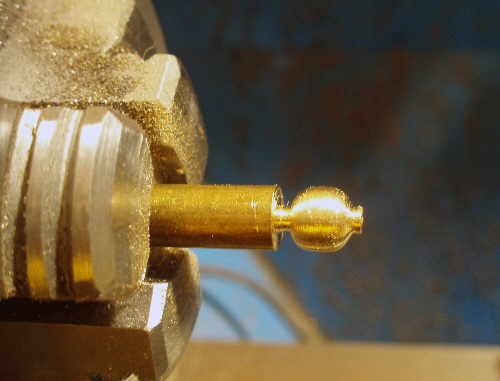
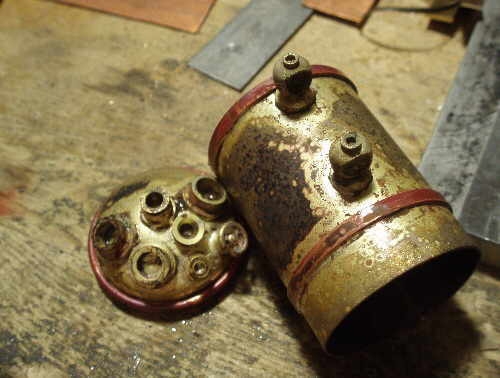
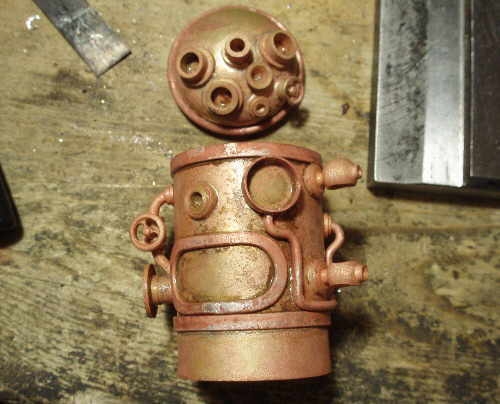
Котел в сборе. Рука набита на флешках, только тут места побольше, есть где разгуляться :-)
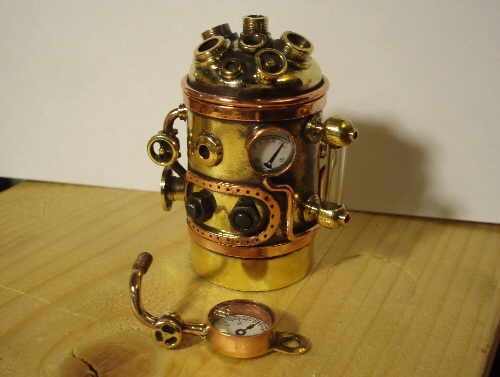
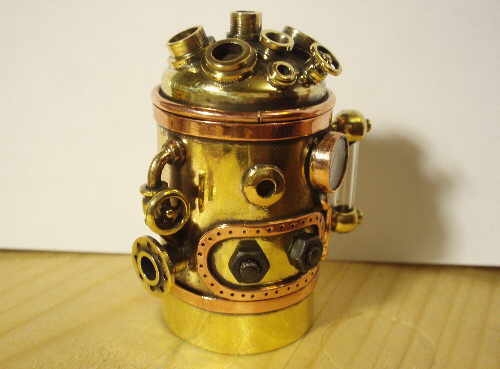
Дополнительный манометр на основном корпусе стапеля:
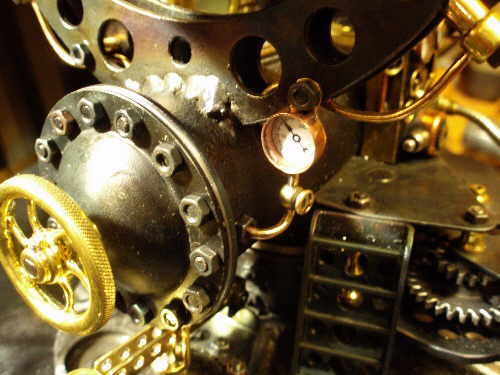
Котел и баллоны соединяются прихотливо изогнутыми трубками. Чтобы медная трубка не сминалась на малом радиусе, гну вокруг специально выточенной роликовой оправки, через несколько промежуточных отжигов. Оправка не дает трубке сплющиваться, расползаться в ширину при сгибании. Таким образом можно обойтись без внутренней забивки песком, канифолью и т.п. веществами, и сохранить правильный профиль трубки на повороте:
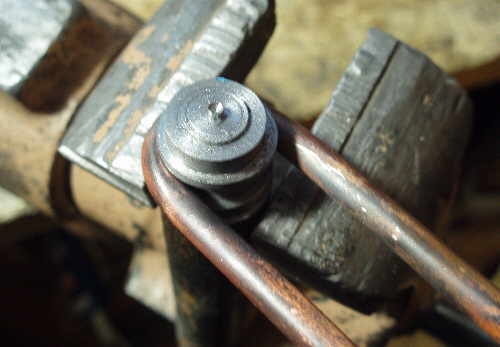
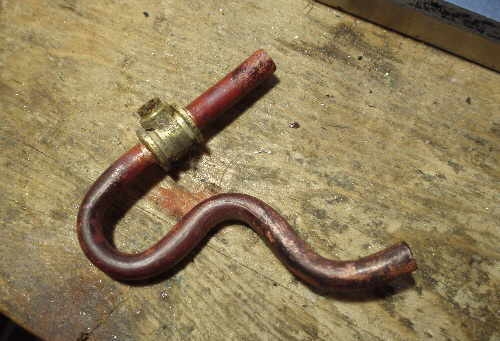
Для разнообразия, эти трубы будут не гладкими, а как бы составлены из отдельных колен. Для имитации стыков напаиваются колечки из мельх. проволоки:
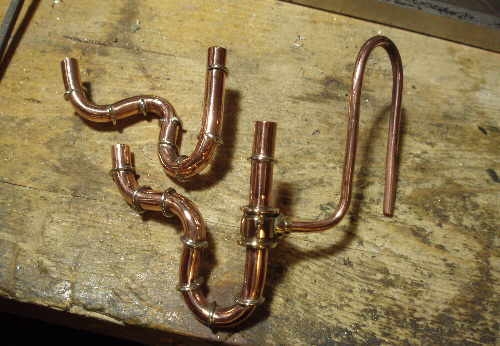
Корпуса «баллонов»:
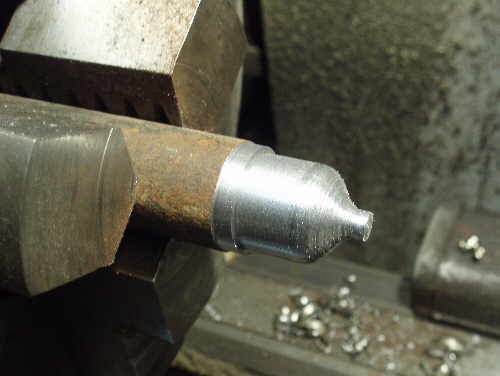
Узел в сборе:
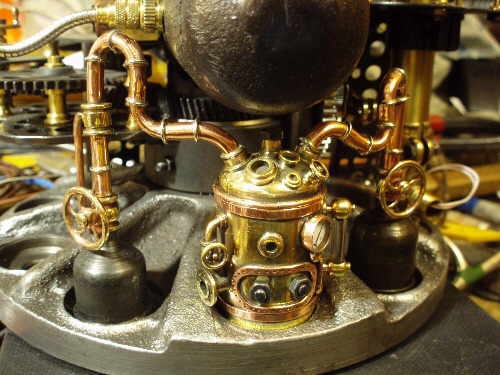
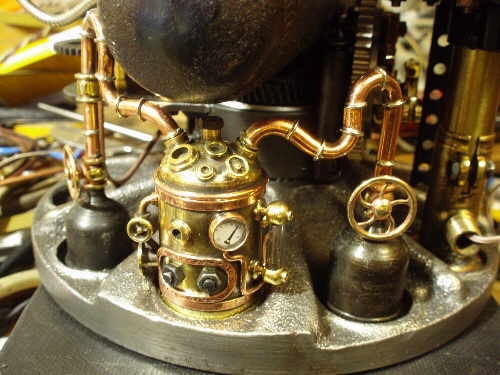
Окончательное соединние трубок с вентилями и крышкой котла произведена на олово, электрическим паяльником.
Теперь незанятыми осталось всего два слота на чугунном диске :-)
Продолжение следует :-)
Предыдущие части ворклога:
steampunker.ru/blog/forsteammaker/5997.html
steampunker.ru/blog/forsteammaker/5998.html
steampunker.ru/blog/forsteammaker/5999.html
steampunker.ru/blog/forsteammaker/6002.html
steampunker.ru/blog/forsteammaker/6006.html
steampunker.ru/blog/forsteammaker/6009.html
steampunker.ru/blog/forsteammaker/6023.html
steampunker.ru/blog/forsteammaker/6095.html
73 комментария
Я не знаю что сказать:)…
А… ну да ..+
Ну, пример: в классической металлообработке, при сверлении обычно заготовка неподвижна, а сверло вращается. Однако, в кухонно-наколенных условиях иногда бывает выгоднее зажать в дрель и крутить заготовку, а неподвижно держать пассатижами сверло…
А в третьих, богатый ассортимент инструмента и приспособлений, в свою очередь мощно стимулирует расширение горизонтов творчества. Когда знаешь, что можно своими силами выполнить и это, и это… и причем — БЫСТРО, через час уже можно будет иметь на руках готовую деталь, и не надо бегать за токарем или сварщиком… все это не может не иметь благотворного влияния на уровень проектов.
Потому что ведь каждому знакомо: еще на уровне первичного проектирования\обдумывания концепции, огромное количество вкусных вариантов приходится отбрасывать по банальной причине — я ТАК сделать не смогу. Придумать, нарисовать — могу, а в металле выполнить — нет. Руки недостаточно прямые, и инструмент не самый подходящий… Не правда ли, у каждого так бывало? :-)
Поэтому изначально, еще на этапе обдумывания концепции, было решено: несколько различных вариантов подсветки — в тему, ибо лампу можно в кач-ве ночника использовать. А вот самодвижущейся кинетики с внутренними моторами — не будет. Отдельные узлы и детали можно потрогать и покрутить руками. И достаточно :-)
За следующие проекты ничего обещать не могу, поживем — увидим :-)
— Да, на самом деле на больших машинах там больше кранов, как минимум 2 отсечных, и 2 продувочных. Однако, миниатюризация диктует некоторую степень упрощения многих узлов.
Я уже писал в одной из прошлых тем, что в этом проекте не стремлюсь к точному копированию, а комбинирую «архетипы», обобщенные визуальные образами.
Так вот, «обобщенная суть образа» водомерного стекла, это прозрачная трубка, вертикально закрепленная за концы. Наличие\отсутствие отсечных краников, это «рюшечки», они концептуально к основному «архетипу» ничего не добавляют. Не знаю, понятно ли объяснил свою кочку зрения…
— Пожалуйста. Действующая модель Стирлинга с водяным охлаждением, видеоролик 24 Мб:
narod.ru/disk/5956391000/P2210897.AVI.html
Лодочный мотор из бензотриммера:
alekssi.narod.ru/Veter/Motor5.html
Главная опасность заключается в том, что войдя в струю ТАКОГО творчества, ни на что другое уже ни руки ни мозги «не стоят» :-)) В результате, встаешь с утра с твердым решением, доделать уже сегодня вполне коммерческий заказ, ибо договорный с заказчиком срок уже близок. И… вместо этого опять берешься точить\паять детали для лодки :-)
а какой горелкой пользуетесь, газ, бензин? и какой припой?
Кстати, без опыта работы с цинком, можно просто брать латунь с высоким содержанием цинка, и сплавлять с серебром 1:1. Если делать быстро, и не перегревать металл, то цинк при такой технологии вообще практически не убегает.
ЛС59-1 применяется для изготовления гаек, болтов, зубчатых колес, втулок. Но те же детали к сожалению изготавливаются и из других марок латуни.
Усилие на ролике зависит от толщины деформируемого металла, и для 0,5 мм желески совсем не велико. Деревянный шаблон легко выдерживает такую нагрузку.
меня, в этот раз, вы порадовали еще и тем что не собираетесь крутить винты и прочее…
а то я побаивался что вы это сделаете и только испортите… Вы совершенно правы! в этой работе движение лишнее…
Оценки дело неблагодарное, но плюсую с удовольствием!
А как Вы сделали накаточку на вентиле? Можно ли сделать подобное без механизации?
Без механизации вряд ли получится, давление ролика на заготовку довольно приличное надо организовать. Но если очень хочется, я бы наверное попробовал на основе стандартного роликового трубореза организовать, заменив режущий нож-ролик на зубчатый, типа колеса от зажигалки.
А вот за идею с труборезом спасибо огромное!
На работе сегодня запчасти от станка выкинули, тащу понемногу домой:)
Так виртуозно и задвижки, и колена, а сколько времени прошло с начала работы?
Посмотрел датировку файла CDR-эскиза лодки в трех проекциях — можно считать его началом работы над проектом? 13 сентября 2011.
Котёл сказка! +
steampunker.ru/uploads/images/00/37/53/2012/02/17/e78e13.jpg
steampunker.ru/uploads/images/00/37/53/2012/02/17/5d89c2.jpg
Вот будет вещь полностью готова, сделаю итоговую фотосессию хорошим аппаратом, и выложу отдельной темой.